Author: MCT Groups
Join MCT Group Limited at Metef Exhibition 2025!
- Home
- Join MCT Group Limited at Metef Exhibition 2025!
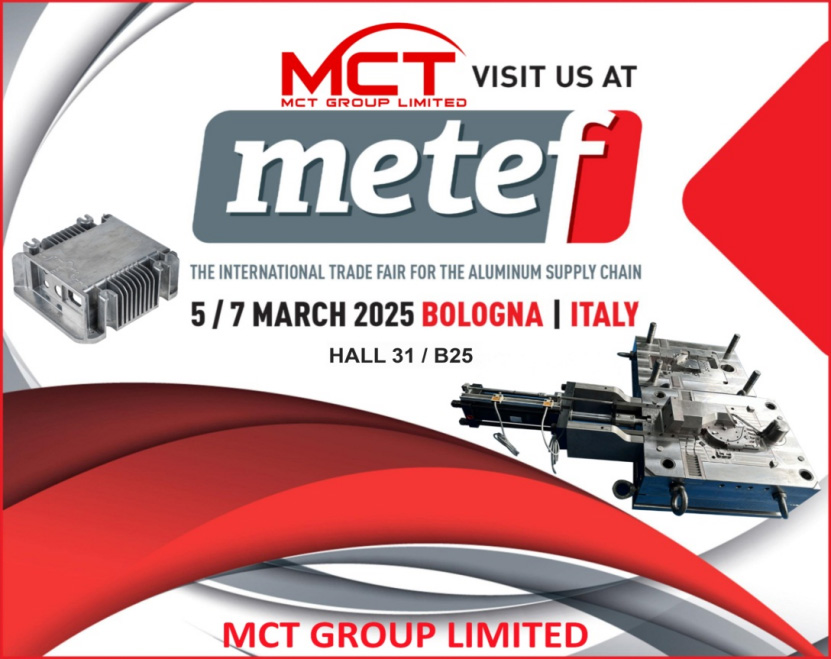
Join MCT Group Limited at Metef Exhibition 2025!
We are thrilled to announce that MCT Group Limited will be exhibiting at Metef 2025 from 5th to 7th March! Visit us at Stand B25, Hall 31 to explore our expertise in high-pressure die casting mold tool manufacturing and precision casting in Aluminum, Magnesium, and Zinc.
Metef is the perfect platform to connect, exchange ideas, and discover new opportunities in the die casting industry. Whether you need high-quality mold tools or precision casting solutions, our team is ready to discuss how we can support your projects.
Looking forward to meeting you there! Let’s shape the future of die casting together.
hashtag#Metef2025 hashtag#DieCasting hashtag#MCTGroup hashtag#Manufacturing hashtag#CastingSolutions hashtag#MoldTools hashtag#Aluminum hashtag#Magnesium hashtag#Zinc hashtag#Networking hashtag#Innovation
Stamping Die Parts- A Major Aspect of Sheet Metal Forming
- Home
- Stamping Die Parts- A Major Aspect of Sheet Metal Forming
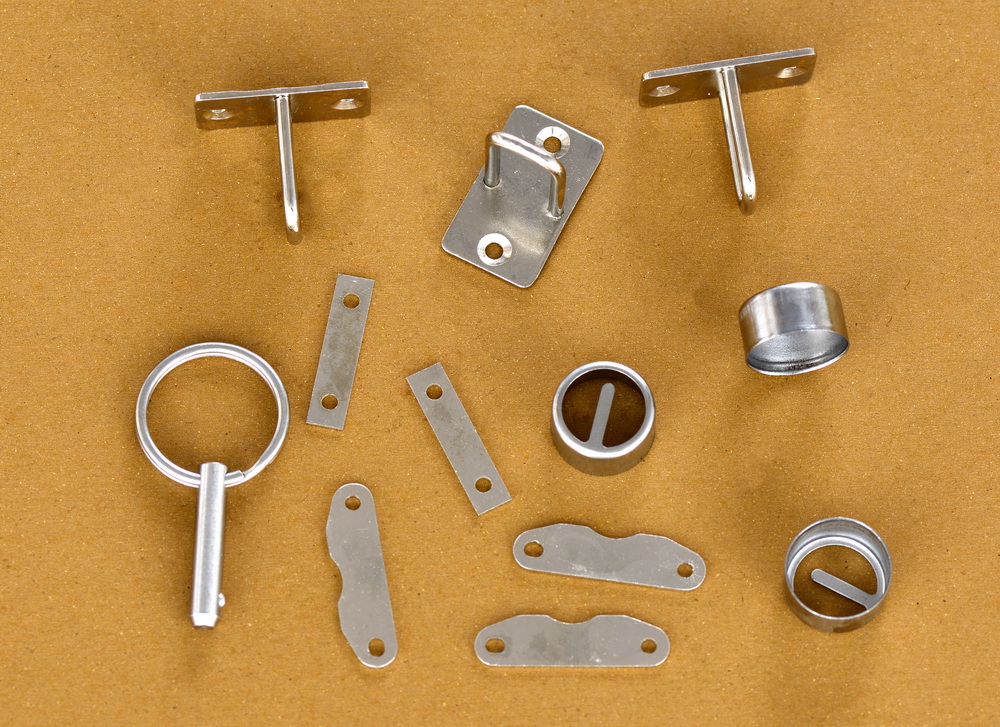
Stamping Die Parts- A Major Aspect of Sheet Metal Forming
Massive presses known as stamping presses are utilized to perform the stamping procedure. Mechanical, hydraulic, and mechanical servo presses are the three most often utilized types of presses. Typically, these presses are attached to a feeder that automatically feeds coils or blank sheet metal through the press. The components of the stamping dies and stamping presses are described here.
These stamping die components are described below in brief.
Shoes, die plates, and die sets: These are the same size as the die and are composed of steel or aluminum. Together, these three serve as the cornerstone of functional stamping die components. These stamping die parts must be ground or machined to maintain their parallelism and flatness. Because it is more resilient, lightweight, and easily machined, aluminum is a fantastic material for these stamping die components. Die pins are used to secure the upper and lower die shoes that make up the stamping die set. The amount of pressure on stamping die parts China that is anticipated throughout the cutting and carving operation determines the thickness of the stamping die shoe.
Guide pins and bushings:
Both of these aids in maintaining the alignment of the upper and lower stamping die shoes. They come in two fundamental varieties: friction pins and bearing style pins. They are both quite small. Hardened steel is used to make these pins, while aluminum-bronze is used to make the bushings. The top and lower stamping die shoes may be separated thanks to these pins, which also serve to lessen friction.
Heel Plates and Blocks:
The upper and lower stamping die shoes are attached to steel heel blocks. Any side pressure that could be created during the cutting and carving operation is lessened by the wear plates inside of them. These blocks are necessary because force applied from a single direction may bend the guide pins and increase the possibility of incorrect alignment throughout the procedure.
Keys, dowels, and screws:
Screws are used to secure the top and lower die shoes. Dowels assist in putting the die shoes in their proper location. Steel keys are used to locate die portions and their stamping die parts.
Injection Molding in China: The Key to Efficient Manufacturing
- Home
- Injection Molding in China: The Key to Efficient Manufacturing
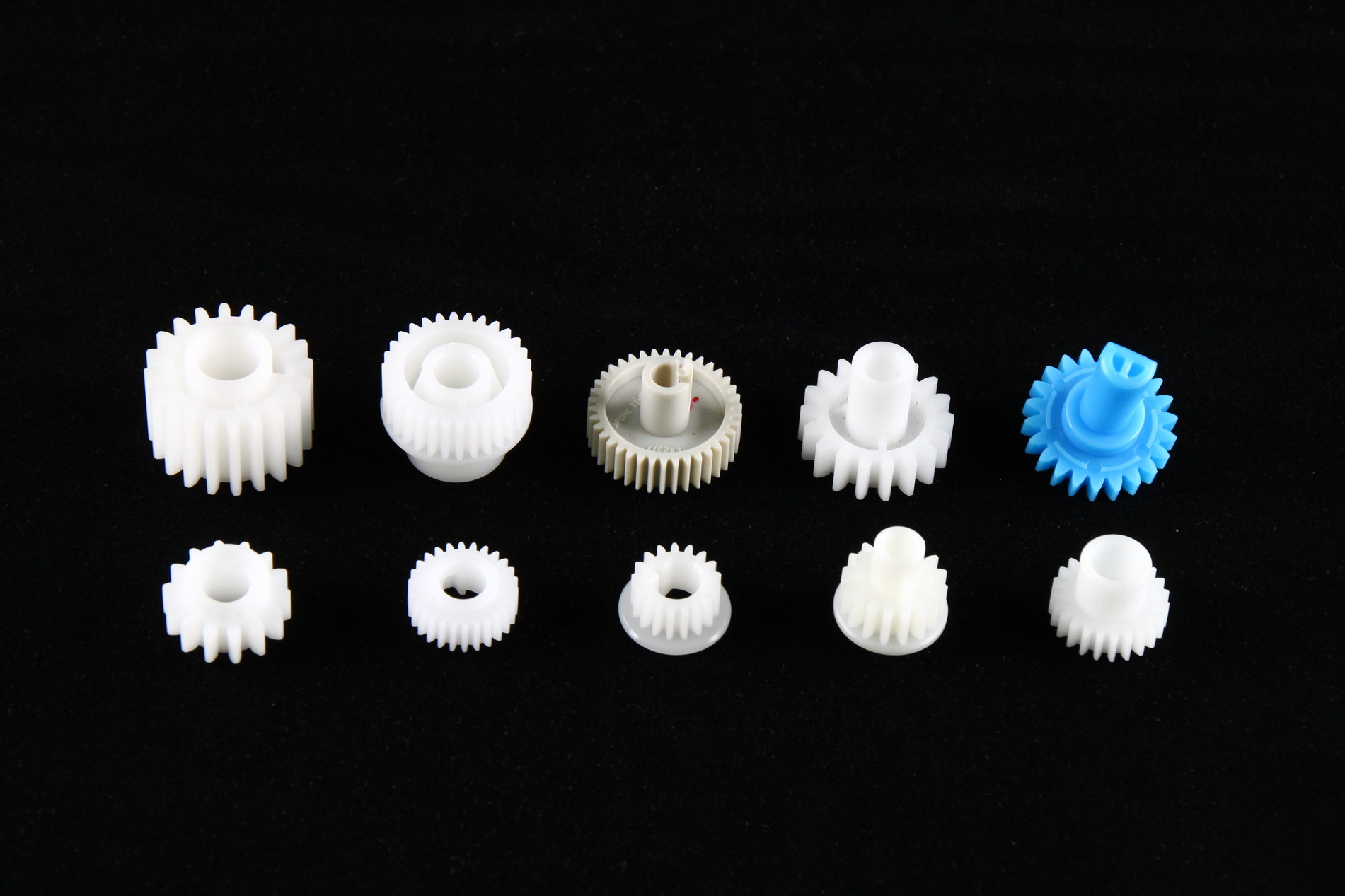
Injection Molding in China: The Key to Efficient Manufacturing
Infusion forming is one of the most broadly utilized assembling processes across different ventures. It includes infusing liquid material — frequently plastic — into a form to make exact and complex shapes. China has turned into a worldwide center point for infusion shaping because of its trend setting innovation, practical creation, and tremendous skill. This blog investigates why China has turned into the go-to objective for infusion shaping administrations.
Cost Effectiveness
One of the main benefits of infusion forming in China is the expense productivity. Work and material costs in China are by and large lower than in numerous Western nations, making it a more reasonable choice for organizations looking for great assembling. This permits organizations to create enormous amounts of items for a portion of the value they would pay somewhere else.
Excellent Principles
In spite of the lower costs, the nature of items made in China remains particularly high. Chinese makers have taken on cutting edge infusion forming advances and works on, guaranteeing that the end results satisfy worldwide quality guidelines. Numerous plants are ISO-guaranteed, and they utilize talented architects and specialists to guarantee accuracy in each part created.
Speed and Adaptability
China’s infusion shaping industry is known for its speedy completion times. With exceptionally streamlined creation frameworks, Chinese makers can deliver models and huge scope runs with insignificant lead times. This speed can be urgent for organizations hoping to lessen time-to-showcase for their items. Furthermore, Chinese producers offer a serious level of adaptability, considering customization and changes as expected by clients.
A Wide Scope of Materials
China’s infusion forming industry isn’t restricted to simply plastic. Makers have the capacity to work with a wide assortment of materials, including metals, elastic, and, surprisingly, biodegradable plastics. This adaptability permits organizations to pick the best material appropriate for their particular necessities, whether it’s sturdiness, adaptability, or ecological benevolence.
Prototyping and Tooling Mastery
China is likewise known for its prototyping and tooling mastery. Infusion shaping requires exact molds, and Chinese producers have created progressed tooling capacities to make complex molds at serious costs. This guarantees that organizations can rapidly test models before large scale manufacturing, limiting the gamble of exorbitant mix-ups during the assembling system.
Worldwide Inventory network Mix
China’s broad organization of providers and coordinated factors framework guarantees that infusion shaped parts can be conveyed universally easily. This worldwide store network guarantees that organizations, no matter what their area, can get to Chinese makers for infusion trim and advantage from their savvy and excellent administrations.
Infusion forming in China gives organizations a one of a kind mix of moderateness, quality, speed, and adaptability. As the nation keeps on putting resources into cutting edge innovations and framework, China’s situation as a forerunner in the worldwide infusion forming market is supposed to reinforce. For organizations hoping to scale their assembling, China stays an optimal decision to meet their creation needs.
Rapid Prototyping in China: Streamlining Product Development from Concept to Final Design
- Home
- Rapid Prototyping in China: Streamlining Product Development from Concept to Final Design
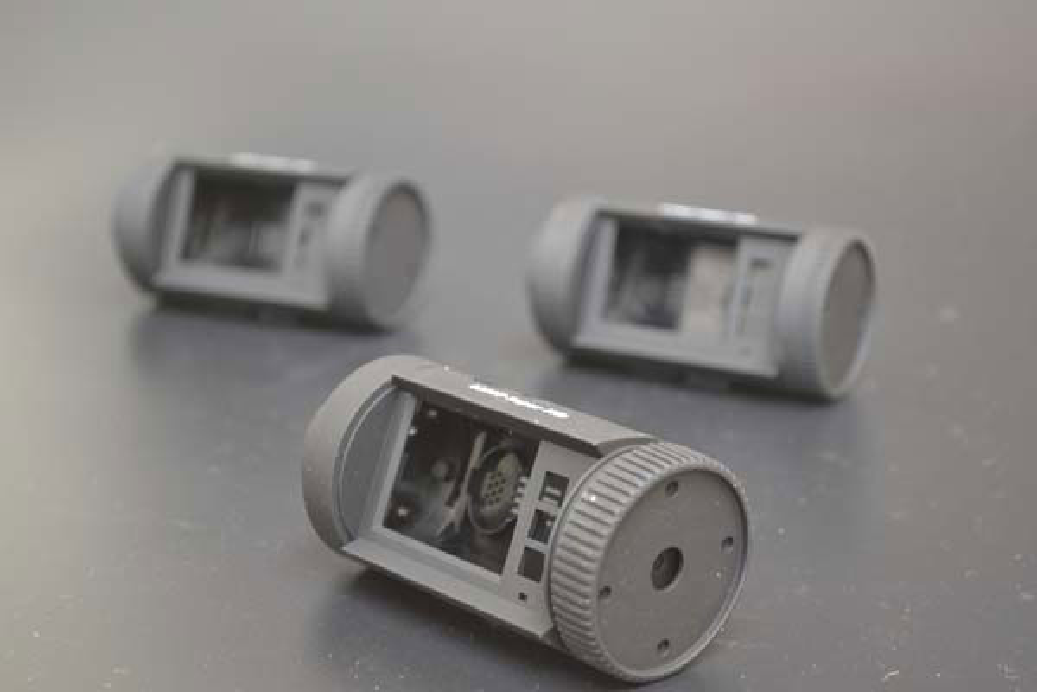
Rapid Prototyping in China: Streamlining Product Development from Concept to Final Design
The collection of methods known as rapid prototyping is used to swiftly turn a three-dimensional design into a physical part or assembly. By iterating several times between digital designs and physical prototypes in a quick and economical workflow, engineers and designers may produce a superior end product through rapid prototyping. The best part is that 3D printed prototypes are inexpensive, allowing teams to quickly produce dozens of reasonably priced prototypes.
Prototyping versus Rapid Prototyping
Product engineers and designers would use simple equipment to manufacture improvised proof-of-concept models, but the same procedures that were used to produce functioning prototypes and production-quality parts were frequently needed. Low-volume, customized prototypes are unaffordable due to the high setup and tooling costs associated with traditional production techniques like injection molding.
Rapid prototyping China, on the other hand, takes items through a number of validation steps before mass production, helps businesses swiftly transform ideas into realistic proofs of concept, and progresses these concepts to high-fidelity prototypes that look and function like final products.
With rapid prototyping, engineers and designers can produce prototypes straight from CAD software digital models more quickly than ever before. They can also make quick, frequent changes to their ideas in response to input and testing in the real world.
Benefits of Quick Prototyping
Acknowledge and investigate ideas with ease, rapid prototyping transforms early concepts into low-risk concept explorations that quickly take on the appearance of finished goods. It enables designers to move beyond virtual visualization, which facilitates side-by-side idea comparison and comprehension of the design’s appearance and feel.
Design Iteratively and Immediately Adjust for Modifications
Before reaching a final product, design is usually an iterative process that involves several iterations of testing, assessment, and improvement. Rapid prototyping with 3D printing elevates this important trial and error process by offering the ability to produce more realistic prototypes more quickly and make changes quicker.
Reduce Design Flaws and Conduct Extensive Testing
Early detection and correction of design defects can help businesses avoid later, expensive tooling adjustments and design revisions. Rapid prototyping lowers the risk of usability and manufacturability problems before going into production by enabling engineers to extensively test prototypes that resemble final products in both appearance and functionality.
Unveiling the Role of Automotive Low-Voltage Connector Terminals in Intelligent Networking.
- Home
- Unveiling the Role of Automotive Low-Voltage Connector Terminals in Intelligent Networking.
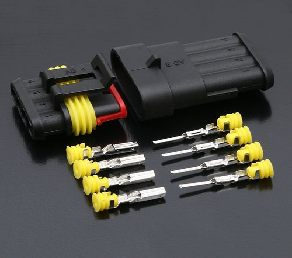
Unveiling the Role of Automotive Low-Voltage Connector Terminals in Intelligent Networking.
The role of automotive low-voltage connector terminals in intelligent networking is pivotal for the efficient operation of modern vehicles. These connectors serve as the physical interface for electrical connections between various vehicle components, facilitating the exchange of data and power.
Data Transmission: Low-voltage connector terminals enable the transmission of data between different electronic control units (ECUs) within the vehicle. This includes communication between the engine control unit, transmission control unit, infotainment system, safety systems, and other onboard devices. By facilitating seamless data exchange, these connectors contribute to the integration of intelligent networking features such as advanced driver assistance systems (ADAS), vehicle-to-vehicle (V2V) communication, and vehicle-to-infrastructure (V2I) communication.
Power Distribution: In addition to data transmission, automotive low-voltage connectors play a crucial role in power distribution throughout the vehicle. They ensure that electrical power from the battery or alternator reaches various components, such as sensors, actuators, pumps, and motors. This is essential for the proper functioning of electronic systems that control vital vehicle functions, including propulsion, braking, steering, and comfort features.
Integration of Advanced Technologies: As vehicles become increasingly connected and autonomous, the demand for advanced technologies continues to rise. Low-voltage connector terminals facilitate the integration of these technologies by providing standardized interfaces for connecting sensors, cameras, LiDAR systems, radar units, and other components essential for autonomous driving and intelligent networking.
Reliability and Durability: Automotive low-voltage connector terminals must meet stringent reliability and durability standards due to the harsh operating conditions encountered in automotive environments. They must withstand exposure to temperature extremes, moisture, vibration, and mechanical stress while maintaining secure electrical connections. Additionally, connectors designed for intelligent networking applications must support high-speed data transmission and comply with industry standards such as CAN (Controller Area Network), LIN (Local Interconnect Network), Flex Ray, and Ethernet.
Scalability and Future-Proofing: As automotive technology continues to evolve rapidly, low-voltage connector terminals must be scalable and adaptable to support future innovations. Manufacturers must design connectors that accommodate increasing data bandwidth requirements, higher power demands, and emerging communication protocols. By investing in versatile connector solutions, automakers can future-proof their vehicles and ensure compatibility with upcoming advancements in intelligent networking.
In summary, automotive low-voltage connector terminals play a crucial role in enabling intelligent networking features in modern vehicles. From facilitating data transmission and power distribution to integrating advanced technologies and ensuring reliability, these connectors are essential components that underpin the functionality and connectivity of next-generation automobiles.
Why do we make a DFM report before making a mold for a plastic mold?
- Home
- Why do we make a DFM report before making a mold for a plastic mold?
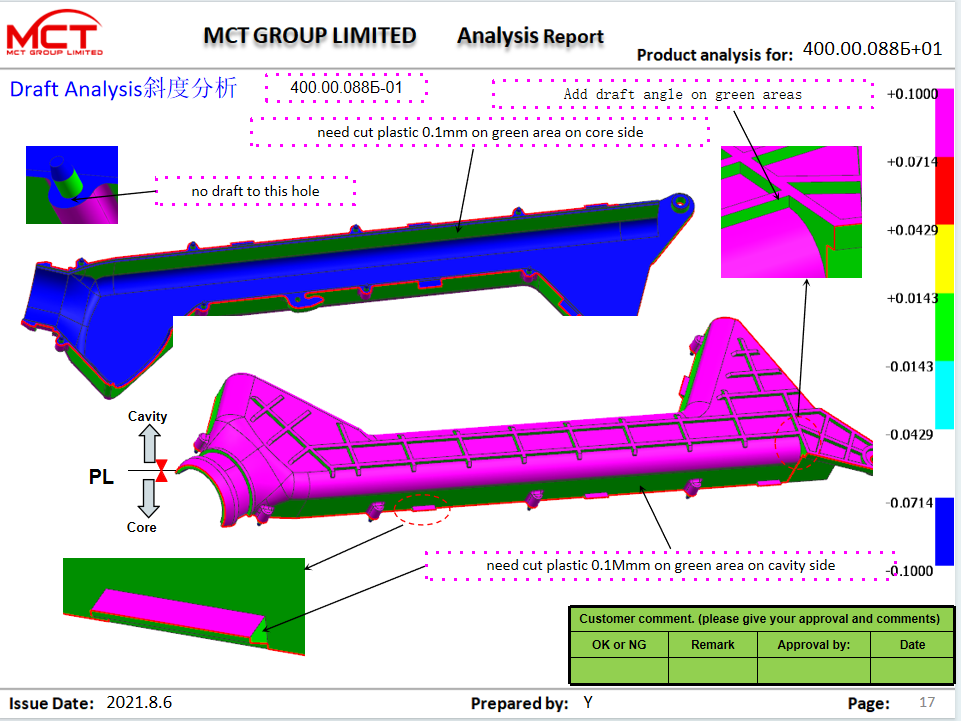
Why do we make a DFM report before making a mold for a plastic mold?
Stamping dies are specialized tools used in metalworking to shape or cut metal parts into specific forms. There are several types of stamping dies, each designed for different purposes:
Blanking Dies: These dies are used to cut flat shapes out of sheet metal. They work by shearing the metal along a defined outline.
Piercing Dies: Similar to blanking dies, piercing dies are used to punch holes through sheet metal. They can create simple round holes or more complex shapes.
Forming Dies: Forming dies are used to bend, stretch, or otherwise shape sheet metal into specific forms. They can be used to create bends, flanges, or other complex geometries.
Drawing Dies: Drawing dies are used to form sheet metal into three-dimensional shapes, such as cups or cylinders. They work by pulling the metal through a die cavity using a punch.
Progressive Dies: Progressive dies are a series of individual dies arranged in a sequence along a single strip of metal. As the metal strip moves through the dies, each operation is performed sequentially, allowing for the creation of complex parts in a single operation.
Compound Dies: Compound dies combine multiple operations into a single die. They are used to perform multiple operations, such as cutting, bending, and forming, in a single press stroke.
Trimming Dies: Trimming dies are used to remove excess material from a stamped part, often after it has been formed or punched. They can be used to trim edges or remove burrs.
Coining Dies: Coining dies are used to create precise, high-quality surface finishes on stamped parts. They can be used to add textures, patterns, or other features to the surface of a part.
These are some of the most common types of stamping dies, but there may be variations or specialized dies used for specific applications within metalworking industries.
What are the benefit of precision casting?
- Home
- What are the benefit of precision casting?
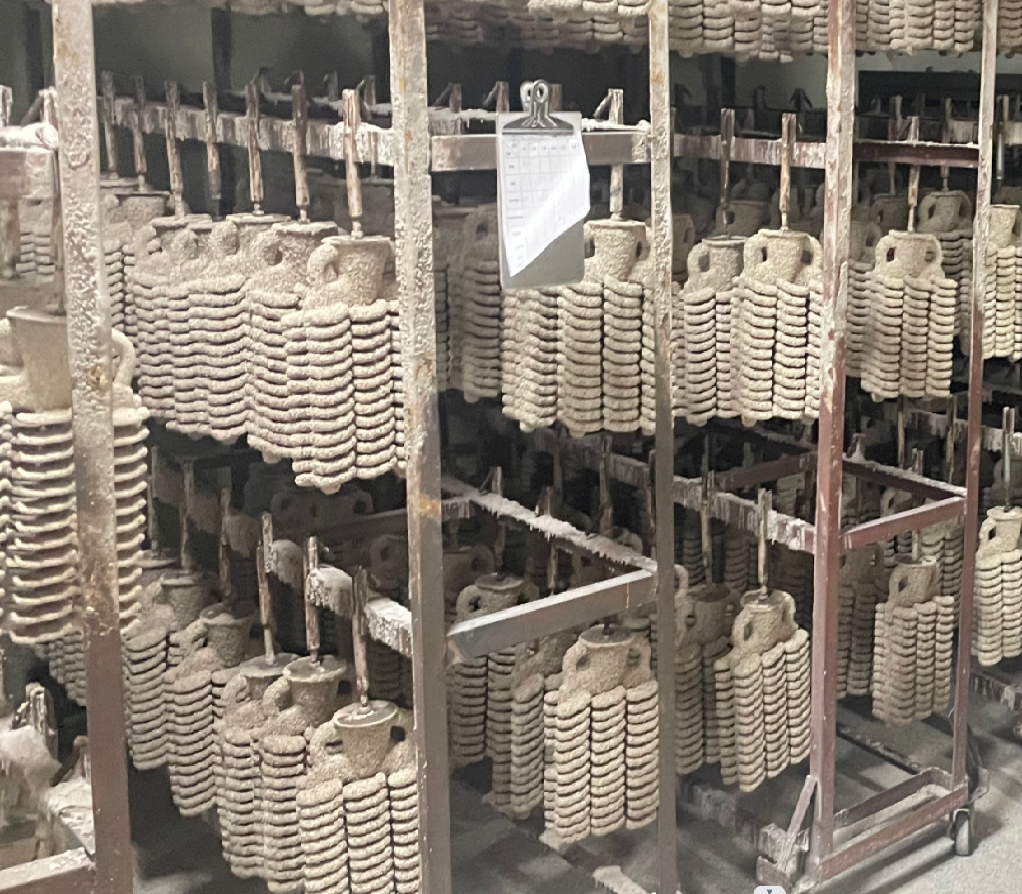
What are the benefit of precision casting?
Precision casting, also known as investment casting or lost-wax casting, offers several benefits in various industries. Here are some of the advantages of precision casting:
Complex Geometries: Precision casting allows for the production of complex and intricate shapes that would be challenging or impossible to achieve through other manufacturing processes. This is particularly beneficial in industries such as aerospace and automotive, where components often have intricate designs.
High Accuracy and Tolerance: The process enables the production of highly accurate and precise parts with tight tolerances. This is crucial in applications where precision is critical, such as in the manufacturing of medical devices or components for high-performance machinery.
Excellent Surface Finish: Precision casting produces parts with excellent surface finish and minimal post-processing requirements. This is advantageous in industries where smooth surfaces are essential, such as in the production of jewelry or components for the food and pharmaceutical industries.
Material Flexibility: Precision casting supports a wide range of materials, including various metals and alloys. This versatility makes it suitable for producing parts with specific material properties, such as strength, corrosion resistance, or heat resistance.
Reduced Material Waste: The process minimizes material waste since the mold material is reusable, and excess material can be melted and reused for other castings. This is an environmentally friendly aspect of precision casting.
Cost-Effective for Small Production Runs: While precision casting can be used for large-scale production, it is also cost-effective for small to medium production runs. This makes it an attractive option for industries that require flexibility in production quantities.
Near-Net Shape Production: Precision casting often produces near-net shape components, meaning that the final product requires minimal additional machining or finishing. This can lead to cost savings and reduced production time.
Design Flexibility: Engineers and designers have greater freedom in designing components with precision casting. The process accommodates intricate and complex designs, enabling the production of customized parts tailored to specific requirements.
Consistency and Reproducibility: Precision casting allows for the consistent and reproducible production of parts, ensuring uniform quality across multiple components. This is essential for industries that demand high reliability and consistency in their products.
Reduced Tooling Costs: Compared to other casting methods, precision casting can have lower tooling costs, especially for smaller production runs. This is because the process relies on a wax pattern rather than expensive molds or dies.
These benefits make precision casting a preferred choice in industries where high precision, complex geometries, and excellent surface finish are critical considerations.
What stamping dies are there?
- Home
- What stamping dies are there?

What stamping dies are there?
Stamping dies are specialized tools used in metalworking to shape or cut metal parts into specific forms. There are several types of stamping dies, each designed for different purposes:
Blanking Dies: These dies are used to cut flat shapes out of sheet metal. They work by shearing the metal along a defined outline.
Piercing Dies: Similar to blanking dies, piercing dies are used to punch holes through sheet metal. They can create simple round holes or more complex shapes.
Forming Dies: Forming dies are used to bend, stretch, or otherwise shape sheet metal into specific forms. They can be used to create bends, flanges, or other complex geometries.
Drawing Dies: Drawing dies are used to form sheet metal into three-dimensional shapes, such as cups or cylinders. They work by pulling the metal through a die cavity using a punch.
Progressive Dies: Progressive dies are a series of individual dies arranged in a sequence along a single strip of metal. As the metal strip moves through the dies, each operation is performed sequentially, allowing for the creation of complex parts in a single operation.
Compound Dies: Compound dies combine multiple operations into a single die. They are used to perform multiple operations, such as cutting, bending, and forming, in a single press stroke.
Trimming Dies: Trimming dies are used to remove excess material from a stamped part, often after it has been formed or punched. They can be used to trim edges or remove burrs.
Coining Dies: Coining dies are used to create precise, high-quality surface finishes on stamped parts. They can be used to add textures, patterns, or other features to the surface of a part.
These are some of the most common types of stamping dies, but there may be variations or specialized dies used for specific applications within metalworking industries.
How to eliminate the internal stress of plastic parts?
- Home
- How to eliminate the internal stress of plastic parts?
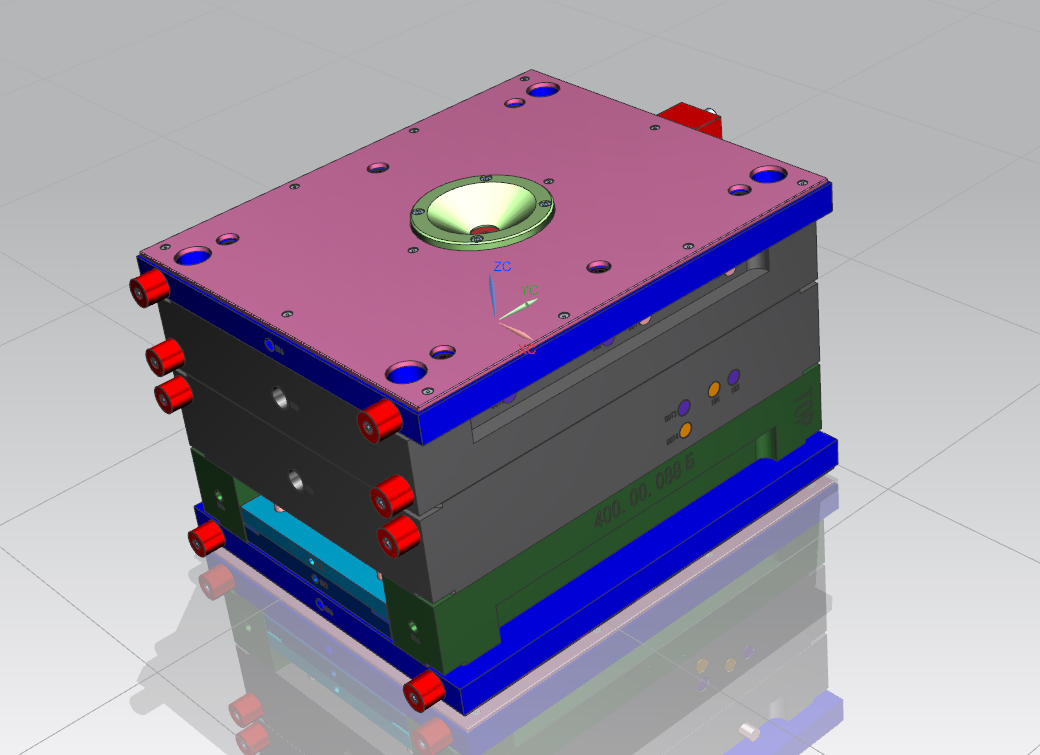
How to eliminate the internal stress of plastic parts?
Precision casting, also known as investment casting or lost-wax casting, offers several benefits in various industries. Here are some of the advantages of precision casting:
Complex Geometries: Precision casting allows for the production of complex and intricate shapes that would be challenging or impossible to achieve through other manufacturing processes. This is particularly beneficial in industries such as aerospace and automotive, where components often have intricate designs.
High Accuracy and Tolerance: The process enables the production of highly accurate and precise parts with tight tolerances. This is crucial in applications where precision is critical, such as in the manufacturing of medical devices or components for high-performance machinery.
Excellent Surface Finish: Precision casting produces parts with excellent surface finish and minimal post-processing requirements. This is advantageous in industries where smooth surfaces are essential, such as in the production of jewelry or components for the food and pharmaceutical industries.
Material Flexibility: Precision casting supports a wide range of materials, including various metals and alloys. This versatility makes it suitable for producing parts with specific material properties, such as strength, corrosion resistance, or heat resistance.
Reduced Material Waste: The process minimizes material waste since the mold material is reusable, and excess material can be melted and reused for other castings. This is an environmentally friendly aspect of precision casting.
Cost-Effective for Small Production Runs: While precision casting can be used for large-scale production, it is also cost-effective for small to medium production runs. This makes it an attractive option for industries that require flexibility in production quantities.
Near-Net Shape Production: Precision casting often produces near-net shape components, meaning that the final product requires minimal additional machining or finishing. This can lead to cost savings and reduced production time.
Design Flexibility: Engineers and designers have greater freedom in designing components with precision casting. The process accommodates intricate and complex designs, enabling the production of customized parts tailored to specific requirements.
Consistency and Reproducibility: Precision casting allows for the consistent and reproducible production of parts, ensuring uniform quality across multiple components. This is essential for industries that demand high reliability and consistency in their products.
Reduced Tooling Costs: Compared to other casting methods, precision casting can have lower tooling costs, especially for smaller production runs. This is because the process relies on a wax pattern rather than expensive molds or dies.
These benefits make precision casting a preferred choice in industries where high precision, complex geometries, and excellent surface finish are critical considerations.